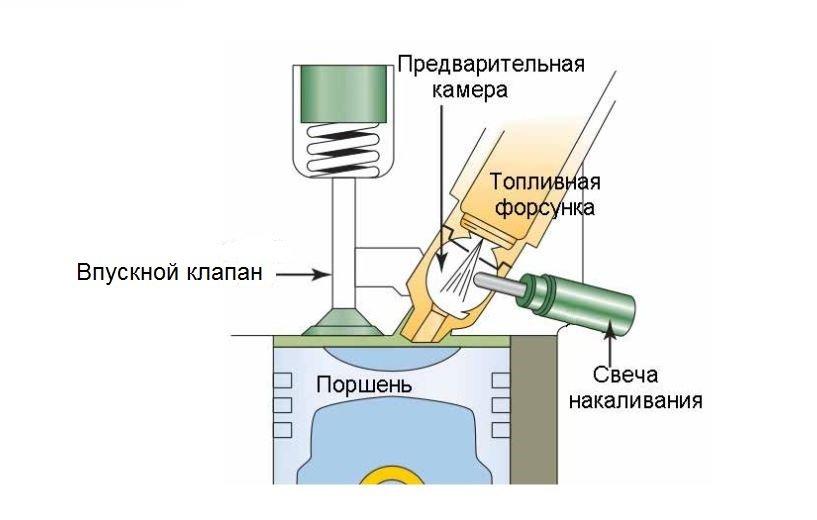
디젤 분사 시스템. 디자인, 장점 및 단점
가솔린 엔진과 달리 디젤 엔진은 처음부터 연료 분사 방식을 사용했습니다. 분사 시스템, 피팅 및 실린더에 공급되는 연료 압력만 변경되었습니다.
일반적으로 디젤 엔진으로 알려진 디젤 엔진의 작동 원리는 가솔린 엔진과 완전히 다릅니다. 연료 트럭에서 연료-공기 혼합물은 피스톤 위의 연소실로 들어갑니다. 압축 후, 혼합물은 스파크 플러그의 전극에서 전기 스파크의 고장으로 인해 점화됩니다. 이것이 가솔린 엔진을 스파크 점화(SI) 엔진이라고도 하는 이유입니다.
디젤 엔진에서 연소실의 피스톤은 엄청난 압력(최소 40bar - 따라서 "고압"이라는 이름)의 영향으로 600-800°C의 온도로 가열되는 공기만 압축합니다. 이러한 뜨거운 공기에 연료를 주입하면 연소실에서 연료가 즉시 자체 점화됩니다. 이러한 이유로 디젤 파워트레인은 압축 점화(CI) 엔진이라고도 합니다. 처음부터 엔진에 공기만 공급하는 흡기매니폴드가 아닌 연소실에 연료를 주입해 공급했다. 연소실이 분할되었는지 여부에 따라 디젤 엔진은 간접 또는 직접 분사 방식의 동력 장치로 나뉩니다.
간접 주입
디젤은 직분사 방식으로 데뷔했지만 오래 사용되지는 않았다. 이 솔루션은 너무 많은 문제를 일으켰고 자동차 산업에서는 1909년 특허를 받은 간접 분사로 대체되었습니다. 직접 분사는 일부 트럭뿐만 아니라 대형 고정식 및 선박용 엔진에 남아 있었습니다. 승용차 설계자들은 작동이 더 부드럽고 소음이 적은 간접 분사 디젤을 선호했습니다.
디젤 엔진에서 "간접"이라는 용어는 간접 분사가 흡기 매니폴드에 공기-연료 혼합물을 분사하는 가솔린 엔진과는 완전히 다른 것을 의미합니다. 간접 분사 디젤 엔진에서 직접 분사 설계와 마찬가지로 인젝터에 의해 분무된 연료도 연소실로 들어갑니다. 연료가 주입되는 보조 부분과 주요 부분, 즉 두 부분으로 나뉩니다. 연료 연소의 주요 과정이 일어나는 피스톤 바로 위의 공간. 챔버는 채널 또는 채널로 상호 연결됩니다. 형태와 기능면에서 챔버는 예비, 와류 및 공기 저장소로 나뉩니다.
후자는 생산이 실제로 중단되었으므로 사용할 수 없습니다. 프리챔버와 스월챔버의 경우 노즐은 보조챔버 옆에 설치되어 연료를 분사합니다. 거기에서 점화가 발생하고 부분적으로 연소된 연료가 메인 챔버로 들어가 그곳에서 연소됩니다. 프리챔버 또는 스월 챔버가 있는 디젤은 원활하게 작동하며 가벼운 크랭크 시스템을 가질 수 있습니다. 그들은 연료 품질에 민감하지 않으며 단순한 디자인의 노즐을 가질 수 있습니다. 그러나 직접 분사 디젤보다 효율이 낮고 연료 소비가 더 많으며 냉각 엔진을 시동하는 데 문제가 있습니다. 오늘날 승용차의 간접분사 디젤 엔진은 과거의 일이었으며 더 이상 생산되지 않습니다. 오늘날 시장에 나와 있는 현대식 자동차에서는 거의 찾아볼 수 없습니다. 인도 힌두스탄과 타타, 러시아 UAZ, 브라질에서 판매되는 구세대 미쓰비시 파제로, 아르헨티나에서 판매되는 폭스바겐 폴로 등의 디자인에서만 볼 수 있다. 애프터마켓 차량에 훨씬 더 많이 사용됩니다.
직접 분사
모든 것은 그와 함께 시작되었습니다. 그러나 직접 주입의 이점은 처음에는 활용되지 않았습니다. 연료의 적절한 소용돌이의 중요성은 알려져 있지 않았고 연소가 최적이 아니었습니다. 그을음 형성에 기여한 연료 덩어리가 형성되었습니다. 피스톤의 프로세스가 너무 빨리 진행되어 엔진이 열심히 작동하여 크랭크 샤프트 베어링이 빠르게 파괴되었습니다. 이러한 이유로 직접 주입을 포기하고 간접 주입을 선호했습니다.
근원으로의 복귀이지만 현대 버전에서는 Fiat Croma 1987 TD가 대량 생산에 들어간 1.9년에만 발생했습니다. 직접 연료 분사는 효율적인 분사 장비, 높은 분사 압력, 우수한 품질의 연료 및 매우 강력한(따라서 무거운) 크랭크셋이 필요합니다. 그러나 이것은 냉각 엔진의 높은 효율과 쉬운 시동을 제공합니다. 직접 분사 디젤 엔진을 위한 최신 솔루션은 주로 완전히 평평한 헤드와 적절한 모양의 챔버(공동)가 있는 피스톤을 기반으로 합니다. 챔버는 연료의 정확한 난류를 담당합니다. 직접 분사는 오늘날 승용차 디젤 엔진에 널리 사용됩니다.
직접 주입 - 펌프 인젝터
기존의 디젤 엔진에서는 다양한 유형의 펌프가 연료 공급을 담당합니다. 개척 시대에는 압축 공기로 연료 분사를 수행했지만 20년대에는 재설계된 오일 펌프로 연료 분사를 수행했습니다. 300년대에는 디젤 엔진용으로 설계된 특수 펌프가 이미 널리 사용되었습니다. 처음에는 저압(최대 60bar)을 생성하는 직렬 펌프를 기반으로 했습니다. 축 방향 분배기(1000bar 이상)가 있는 보다 효율적인 펌프가 등장한 것은 80년대가 되어서였습니다. 524년대 중반에는 기계식 분사 제어를 받았고 1986년대 중반에는 전자식 제어를 받았습니다(BMW XNUMXtd, XNUMX).
이미 30년대에 트럭에 사용된 펌프 인젝터는 연료 분사 방식이 약간 달랐으며 1998년(Passat B5 1.9 TDI) 처음으로 폭스바겐 문제로 승용차에 널리 사용되었습니다. 간단히 말해 펌프 인젝터는 캠축에 의해 구동되는 자체 펌프가 있는 인젝터입니다. 따라서 실린더에 압력을 가하고 주입하는 전체 과정은 실린더 헤드에 국한됩니다. 시스템은 매우 컴팩트하며 펌프를 인젝터에 연결하는 연료 라인이 없습니다. 따라서 노즐 맥동이 없어 연료량 및 누출량 조절이 어렵다. 연료는 단위 인젝터 챔버에서 부분적으로 기화하기 때문에 분사 시기가 짧을 수 있습니다(쉬운 스타트). 그러나 가장 중요한 것은 2000-2200bar의 매우 높은 사출 압력입니다. 실린더의 연료량은 공기와 빠르게 혼합되어 매우 효율적으로 연소됩니다.
일반적으로 단위 인젝터가 있는 디젤은 고효율, 낮은 연료 소비, 고속 및 높은 출력 밀도를 얻을 수 있는 것이 특징입니다. 그러나 단위 인젝터 엔진은 주로 실린더 헤드의 복잡성으로 인해 제조 비용이 많이 듭니다. 그의 일은 힘들고 시끄럽다. 유닛 인젝터로 구동되는 경우 배기 독성 문제도 발생하며 이는 VW가 이 솔루션을 포기하는 데 크게 기여했습니다.
직접 주입 - 커먼 레일
커먼 레일 분사 시스템의 가장 중요한 요소는 펌프가 디젤 연료를 펌핑하는 "가압 연료 축 압기"라고도 하는 탱크 유형인 "커먼 레일"입니다. 펌프에서 직접 노즐로 들어가는 것이 아니라 탱크에서 노즐로 들어가며 각 실린더에 대해 동일한 압력을 유지합니다.
비유적으로, 우리는 각 인젝터가 펌프에서 연료의 일부를 기다리지 않지만 여전히 매우 높은 압력에서 연료를 가지고 있다고 말할 수 있습니다. 인젝터를 작동시키는 전기 충격은 연소실에 연료를 공급하기에 충분합니다. 이러한 시스템을 사용하면 다단계 분사(분사당 8단계까지)를 생성할 수 있으므로 점진적인 압력 증가와 함께 연료가 매우 정밀하게 연소됩니다. 매우 높은 분사 압력(1800bar)으로 인해 거의 안개 형태로 연료를 전달하는 매우 작은 오리피스가 있는 인젝터를 사용할 수 있습니다.
이 모든 것은 높은 엔진 효율, 부드러운 작동 및 낮은 소음 수준(직접 분사에도 불구하고), 우수한 기동성 및 낮은 배기 가스로 보완됩니다. 그러나 커먼 레일 엔진에는 최고 품질의 연료와 최고의 필터가 필요합니다. 연료의 오염 물질은 인젝터를 파괴하고 수리 비용이 매우 많이 드는 손상을 일으킬 수 있습니다.
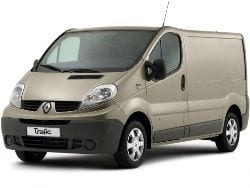
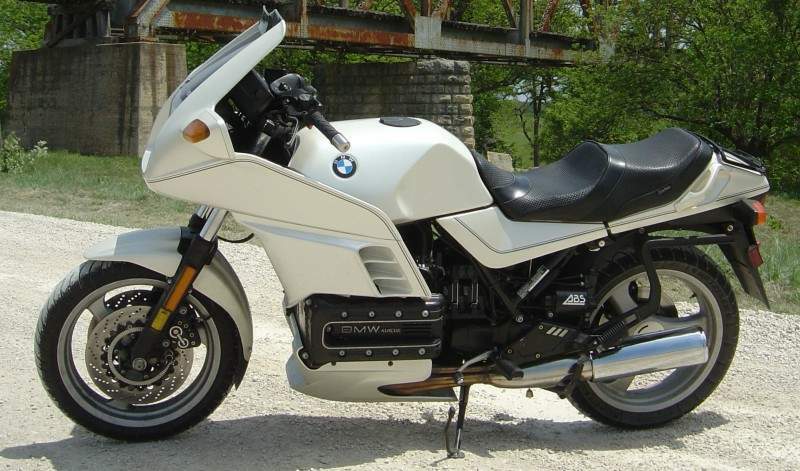